Made in USA, From Sheep to Shelf: Zady’s Feel-Good Sweater
When Maxine Bedat and Soraya Darabi set out to make a wool sweater entirely in the U.S., their first challenge was finding sheep.
A Google search turned up the Imperial Stock Ranch, a 143-year-old sheep and cattle operation in northeastern Oregon. The environmentally conscious ranch owners had a feel-good story that seemed perfect for the entrepreneurs’ brand, Zady, which markets the origins of the products it sells.
But when Ms. Bedat, 32, called from her New York City office, she got a cool reception from ranch owner Jeanne Carver. “She told me that I was from the east and she was from the West; I was a lawyer, she was a farmer; I was young and she was old,” says Ms. Bedat. “She didn’t want to work with me.”
“Made in the USA” is a popular marketing message these days, but much American-made apparel uses fabric and raw materials that are imported. Zady’s young entrepreneurs seized upon the idea of creating a garment entirely in America—wool, spinning, knitting and all. For their socially conscious customers, marketing every aspect of their all-American supply chain would be crucial.
A Sweater’s Journey
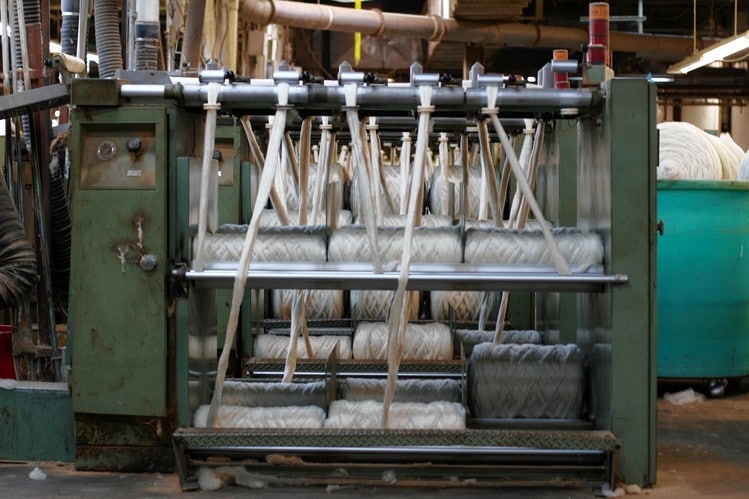
The machine removes natural fibers, leaving behind clean wool that will be spun into yarn OLIVER JEVREMOV
The sweater was Zady’s first foray into manufacturing its own apparel—and a garment its founders hoped would blossom into a full collection. Ms. Bedat and Ms. Darabi started with a classic shape that would come in two shades of heathered gray wool plus a natural white, and a price under $200 that they figured wouldn’t seem outlandish to J. Crew shoppers. The sweater would take the two entrepreneurs on a journey from coast to coast through what remains of the U.S. wool-knit industry, where a few, often family-owned businesses have survived the influx of overseas competition.
Thanks to nimble repositioning, many such old-school businesses are growing again. But they are sometimes caught off guard to find themselves on the cutting edge of fashion, working with a new generation.
Ms. Bedat, who describes herself as a “recovering” lawyer, and Ms. Darabi, a 31-year-old tech entrepreneur, founded Zady in 2013 with the aim of selling well-designed products, from Italian staplers to made-in-Detroit notebooks, while highlighting the companies and artisans behind them. Marketing mixes social media, pop-up stores and a personal approach. “Maxine and I take to social media ourselves,” says Ms. Darabi, who has 398,000 Twitter followers.
The pair won’t reveal Zady’s revenue but say they added 25,000 email subscribers last month and doubled the average order size in the past three months. Zady has drawn venture capital from investors including Google Executive Chairman Eric Schmidt’s Innovation Endeavors, which backed Uber. The two speak in the trendy lingo of tech startups: “There’s something very attractive for our generation about disruption,” Ms. Bedat says.
Their high-octane approach had little appeal to the 61-year-old Ms. Carver, who owns the Imperial Stock Ranch with her husband, Dan Carver.
“She was pushy,” says Mrs. Carver, who took Ms. Bedat’s phone call outdoors, surrounded by 32,000 acres of arid ranch land. “I was like, she’s so removed from our world in agriculture, I don’t think she’s going to get it.”
Ms. Bedat was speaking to the rancher from Zady’s conference room in Manhattan’s Chelsea neighborhood. “I cried,” Ms. Bedat recalls. “My voice got very shaky. I told her that I live in a world where people can wear a sweater and not know wool comes from a sheep.”
Some of Zady’s demands seemed risky or absurd to Mrs. Carver. Not only did Zady’s founders want to reveal all of Imperial’s suppliers, they also wanted to film and photograph the manufacturing process for their website. They pressured the carding, dyeing, spinning and knitting factories to produce the initial batch of 300 sweaters in one month, rather than the ideal two-to-three months. Margins had to be squeezed to meet the sweater’s eventual retail price of $160.
Yet the rancher agreed to take the project on. “She challenged me,” Mrs. Carver says. “She said, ‘Don’t you want to make a difference?’ ”
It may have helped that the Carvers had already worked with a trendy fashion label, which had been drawn to their environmentally friendly, no-till farming methods and their success in saving their sheep business by enlisting American factories to turn their wool into Imperial yarn. Polo Ralph Lauren, stung by criticism of its China-made U.S. uniforms for London’s Olympics, turned to Imperial ranch and its suppliers to make the red, white and blue sweaters U.S. athletes wore in the Sochi Games’ opening ceremony.
Zady might have struggled to make its sweater overseas, where shipping and customs can add months to production and factories require huge minimum orders.
Even with local advantages, the entrepreneurs’ learning curve was high. Still tweaking the design in September, they were aiming to launch the sweater before Thanksgiving.
Imperial’s wool, shorn last spring, was rushed to Jamestown, S.C., in the first week of October. There, Chargeurs Wool USA washed and “carded” it, removing the sort of debris that a sheep picks up on the Oregon range. The mill, founded in 1955, is a unit of the French-owned Chargeurs manufacturer.
“Wool top,” the longest fibers of clean, carded wool, was hurriedly shipped on to Philadelphia, where G.J. Littlewood & Son has had a dye plant since the Civil War, and has been at its current location since 1869. According to Littlewood lore, at one point the family dyed wool for both the Union and Confederacy, says Richard Littlewood, the president and his family’s fifth generation at the plant.
Littlewood has survived by serving up products like industrial yarns for paint rollers, but Mr. Littlewood says new Internet sellers are his company’s main source of growth now. “Since 2013, we’ve got people coming out of the woodwork,” he says.
Mrs. Carver says she wasn’t sure the Zady people recognized how hard everyone was working for their tiny order. The heathered yarn required extra steps and extra time. The gray color had to be reworked twice. “Not only did we do this,” says Mrs. Carver, “we also had to accommodate their filming at every stage of the process.”
In mid-October, the clean, dyed wool was spun into yarn at Kraemer Textiles in Nazareth, Pa., which since its founding in the 1880s has shifted from making silk hosiery to carpet threads and fibers for car-buffing pads.
By late October, the yarn raced across the country to Ball of Cotton, a Los Angleles knitting factory founded 24 years ago by Eddy Park, a 61-year-old Korean immigrant, and his wife, Elizabeth. Ball of Cotton knitted the Polo Olympic sweaters.
Zady’s sweaters launched last week, right on schedule. Back in Oregon, the Carvers’ sheep are sporting next spring’s wool crop. In the past 14 months, 75 American designers have inquired with them for a U.S. yarn source—up from zero in 2009.
Mrs. Carver says she feels she and Zady have more common ground than she once realized. “We’re growing because people want to reconnect to the source of food and fiber and apparel,” Mrs. Carver says. “Food led the way, now apparel is coming on strong.”
Leave a Reply
Want to join the discussion?Feel free to contribute!