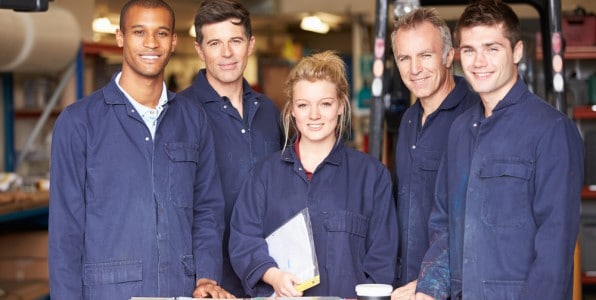
Attracting Future Generations of US Manufacturing Workers
We’ve got a real problem on our hands in America. A gap’s growing between US manufacturing workers set to retire in the next 10 to 15 years and those on the other end of the spectrum. Despite the exciting and innovative things happening…
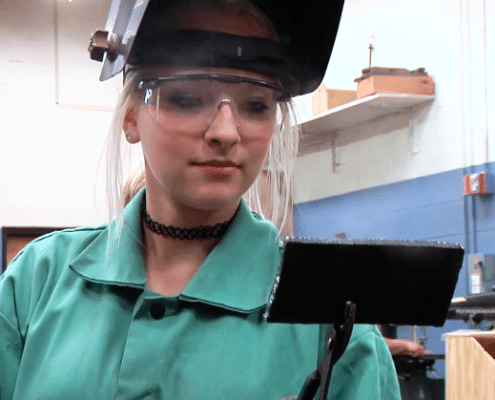
College Degree Not Necessary In Today’s Job Market
At a steel factory dwarfed by the adjacent Auto Club Speedway, Fernando Esparza is working toward his next promotion.
Esparza is a 46-year-old mechanic for Evolution Fresh, a subsidiary of Starbucks that makes juices and smoothies. He’s…
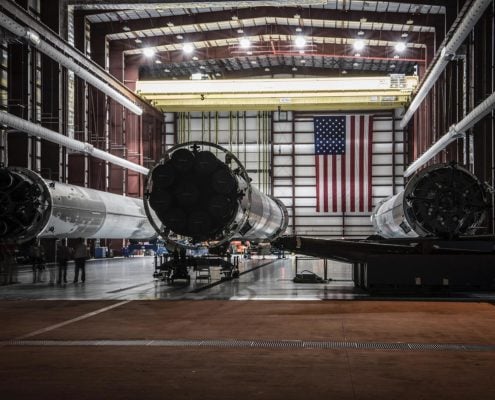
Will The Skills Gap Impact Advanced Manufacturing In Small Town USA?
Most of us, regardless of our age, have heard the song popularized by Sophie Tucker and Eddie Cantor after World War I: “How Ya Gonna Keep ‘Em Down on the Farm (After They’ve Seen Paree?).”
According to Wikipedia, “The lyrics highlight…
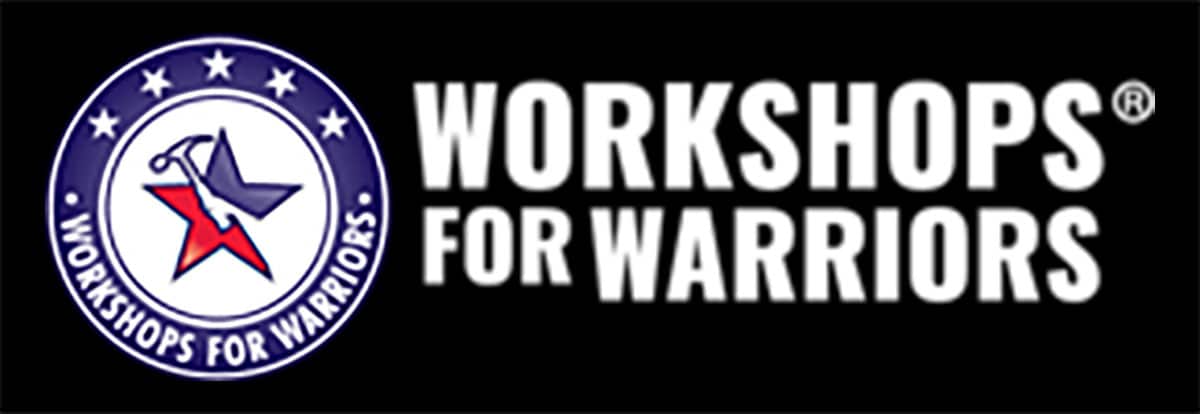
The Advanced Manufacturing Landscape: How Veterans are Saving the Day
Advanced manufacturing is already one of the most in-demand industries in America due to workforce retirements and natural business growth, but it’s also an industry with a severe shortage of skilled workers.
When you pair that with the…
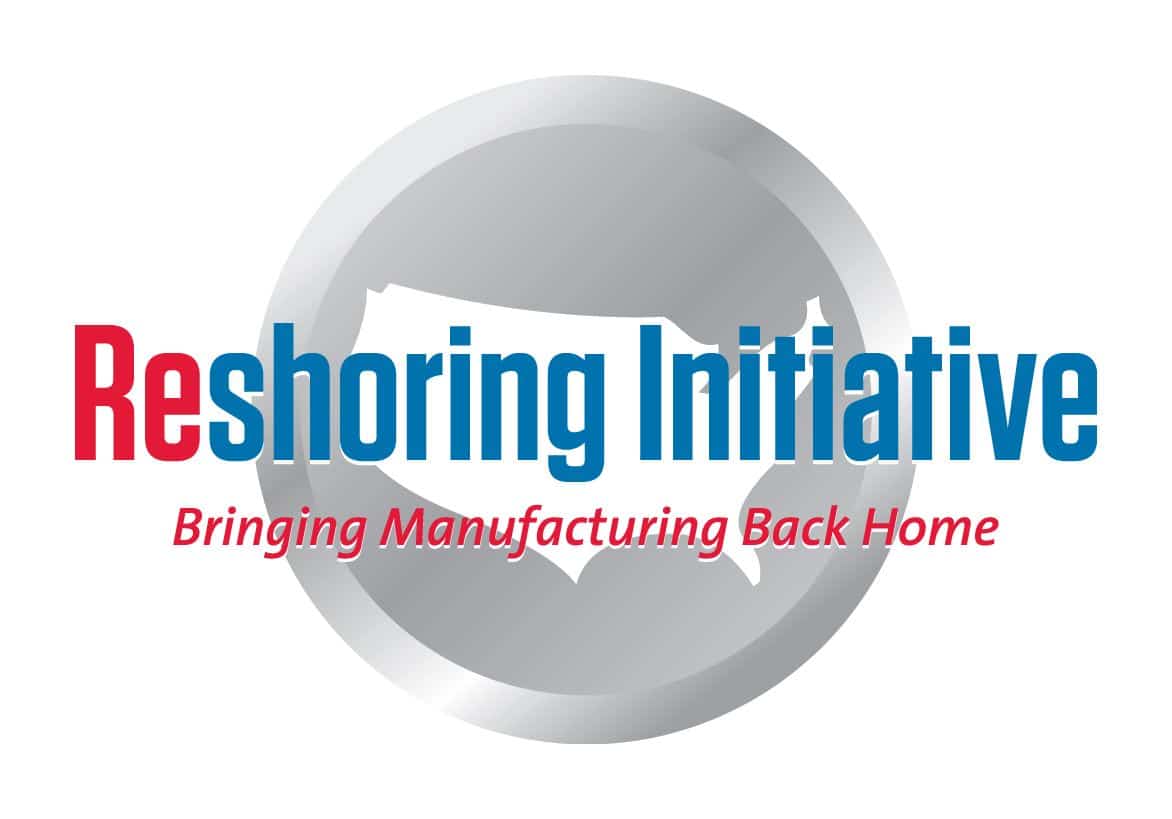
How The U.S. Could Bring Back Manufacturing American Jobs
Many companies that offshored manufacturing American jobs didn’t really do the math.
For decades, U.S. companies have been chasing cheap labor offshore and then importing products to sell in the U.S. market.
Now, a broader focus on…
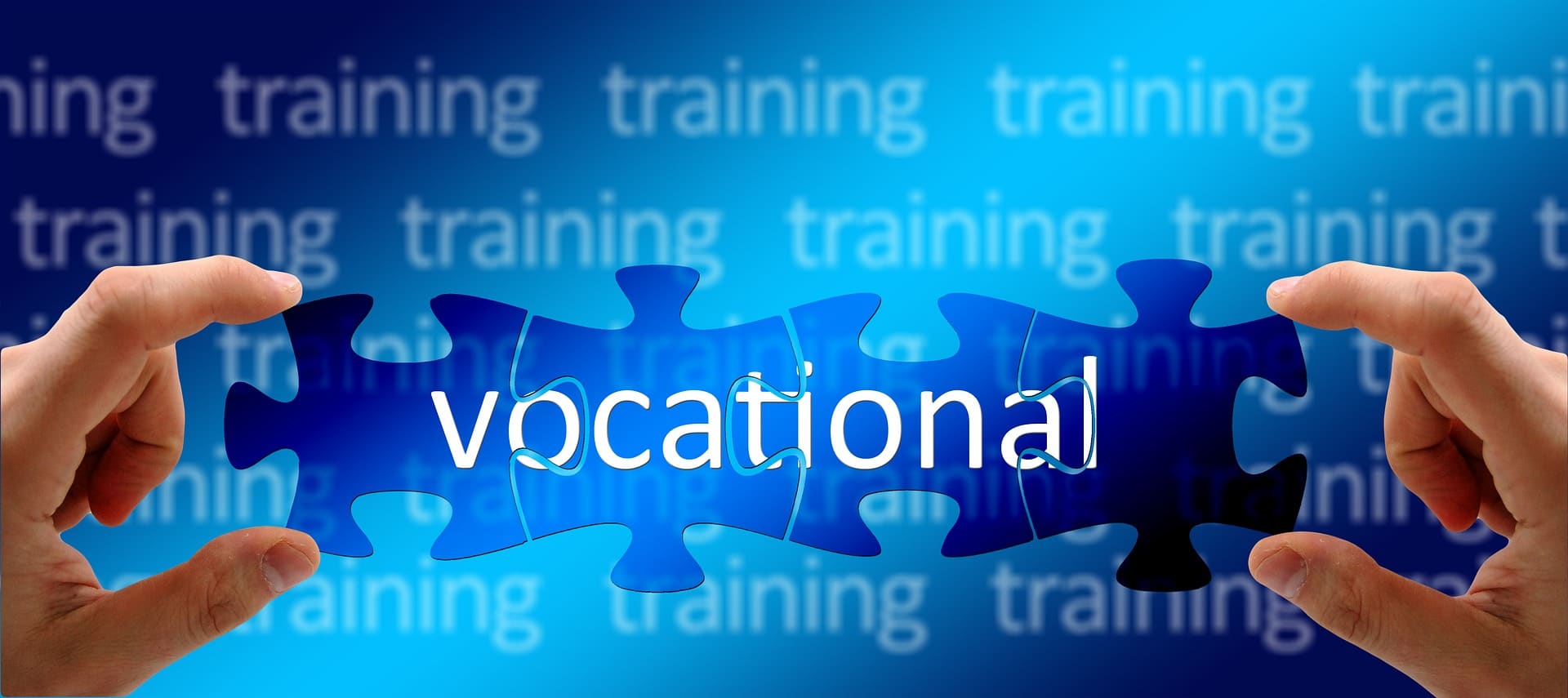
Why We Desperately Need To Bring Back Vocational Training In Schools
Throughout most of U.S. history, American high school students were routinely taught vocational and job-ready skills along with the three Rs: reading, writing, and arithmetic. Indeed readers of a certain age are likely to have fond memories…
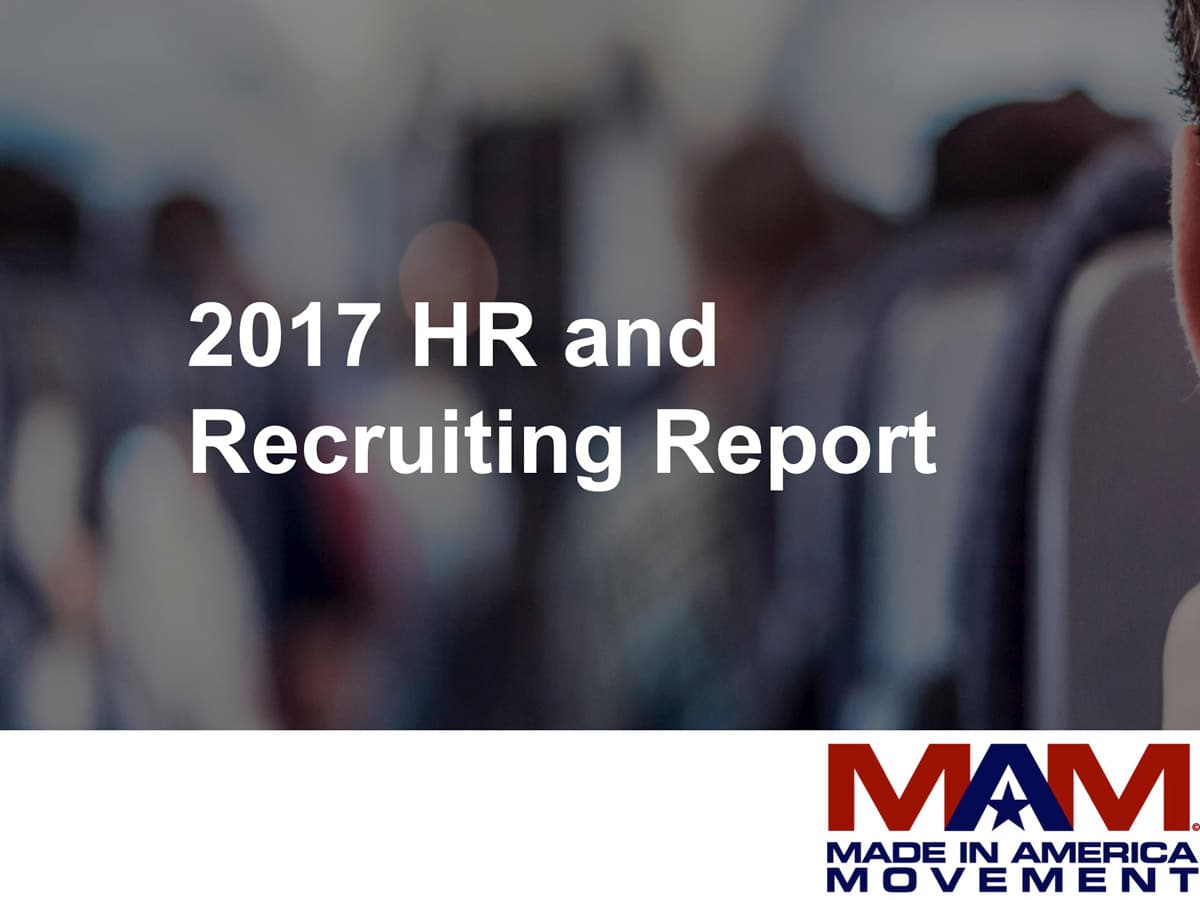
2017 Human Resources & Recruiting Report
Download the 2017 HR and Recruiting Report summary for free. Dive deeply into the questions and facts organizations need to ask to hire the best efficiently.
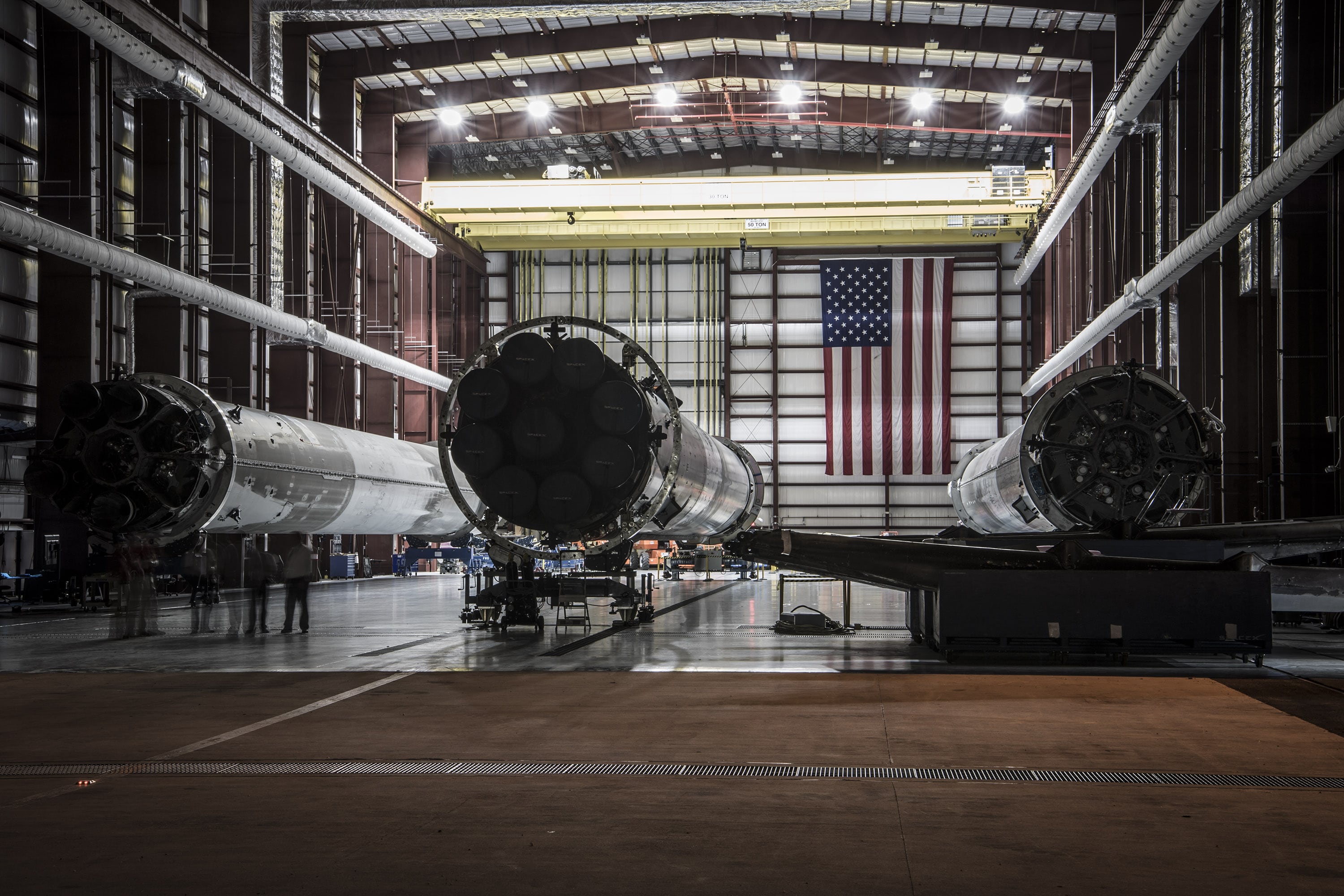
Skills Gap: Aging Workforce Puts Strain on Skilled Manufacturing Workers
General Electric runs two plants in a small New Hampshire town just south of the state's capital, employing 800 workers. GE Aviation is the largest employer in town, with skilled workers building jet engines for the world's major airlines, reports…
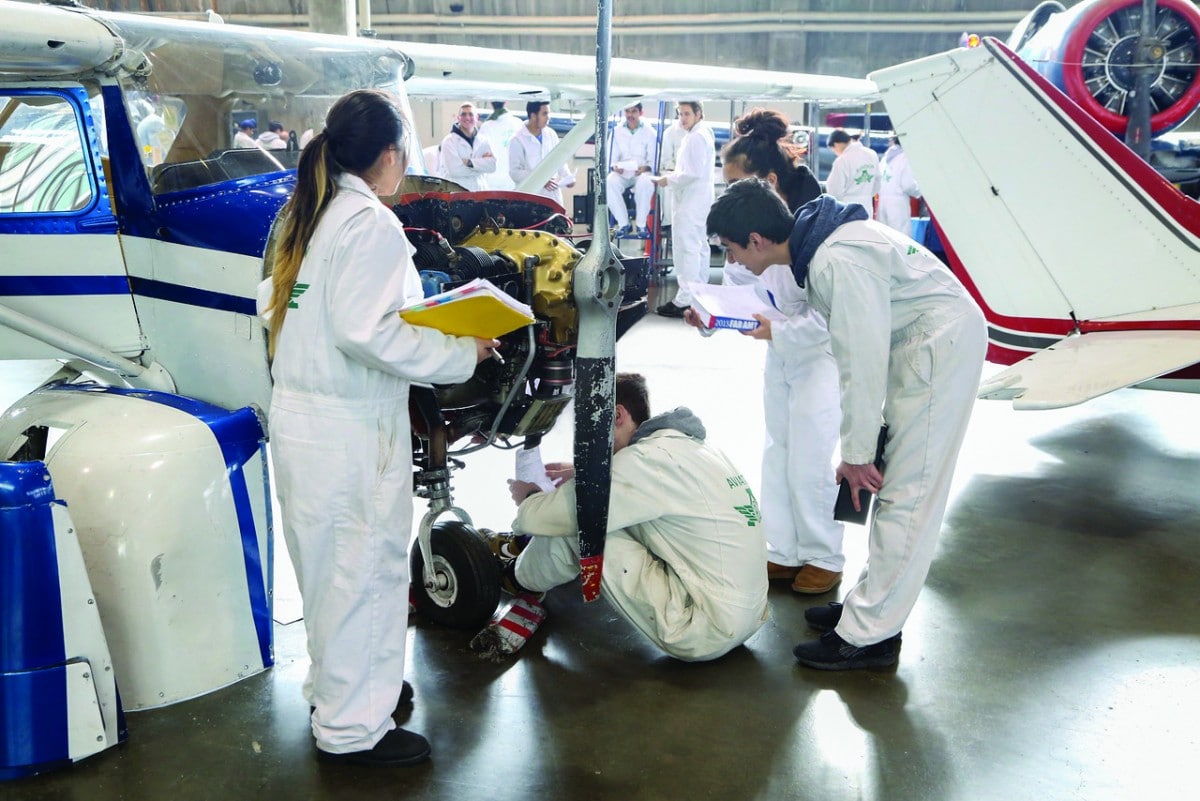
Made In America: $75 Million Grant Helps Students Gain Technical Skills Employers Need
When you back up a commitment with $75 million, people tend to pay attention. I’m certainly paying attention to New Skills for Youth (NSFY), the $75 million grant initiative sponsored by JPMorgan Chase to change the way we approach career…
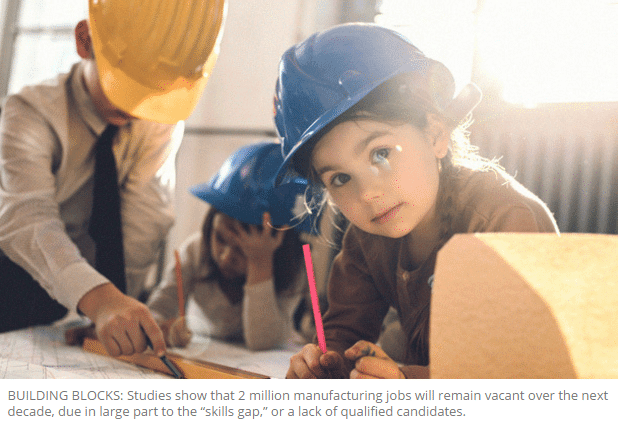
Education: 5 Ways to Inspire the Next Generation of Manufacturers
HIGHER EDUCATION The importance of manufacturing to our economic well-being is not a mystery to the manufacturing industry. But how can we get today’s youth to see the value of a manufacturing career?
There is a surprising yet nevertheless…