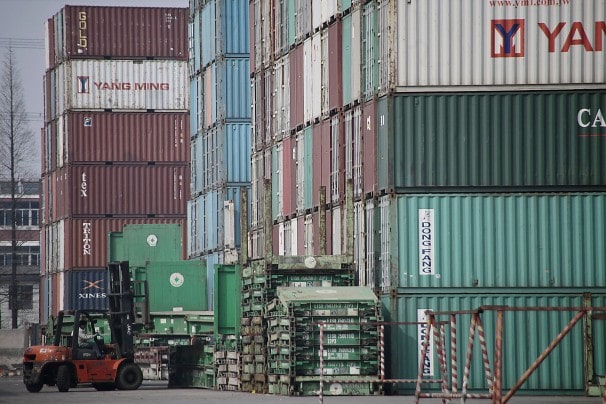
With Exports Rising, US Cities Expand Their Global Footprint
It's well-known American jobs have been lost to overseas competition. While work on U.S. manufacturing floors has declined, overseas markets have developed a growing appetite for American-made goods—from chemicals and wood products, to…
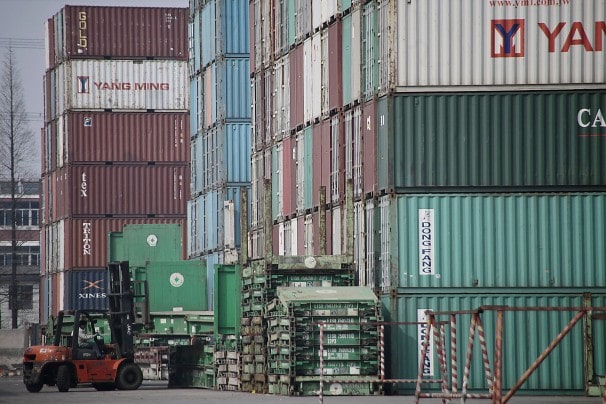
Documentary: Made by China in… America?
Documentary: Made by China in America? directed by Miao Wang about Chinese firms bringing manufacturing to the U.S. It is part of Morgan Spurlock's "We the Economy" series (www.wetheeconomy.com).
When I was a baby, my mom waited in line…
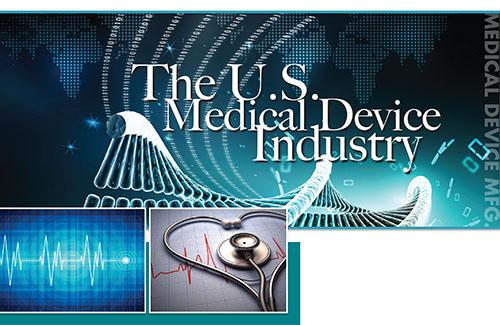
The U.S. Medical Device Industry
The United States remains the largest medical device market in the world with a market size of around $110 billion, and it is expected to reach $133 billion by 2016. The U.S. market value represented about 38 percent of the global medical…
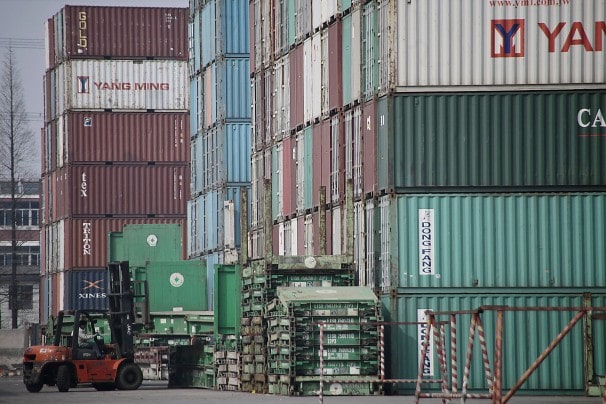
Toy Maker To Bring Lincoln Logs Production Back to U.S.
Production of Lincoln Logs coming back to U.S.A. Manufacturing will once again be made in the U.S.A. (Photo courtesy of K’NEX Brands)
A Montgomery County manufacturer of plastic injection molds and K’NEX construction…
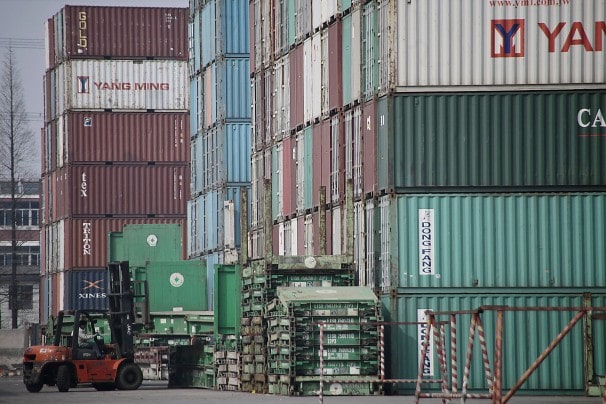
Lincoln Logs to be ‘Made in USA’ Again Creating Jobs in the Process
Lincoln Logs, the popular building toy created nearly a century ago by a son of architect Frank Lloyd Wright, is coming home to the U.S. Maine Gov. Paul LePage announced the logs, used by generations of kids to create miniature buildings,…
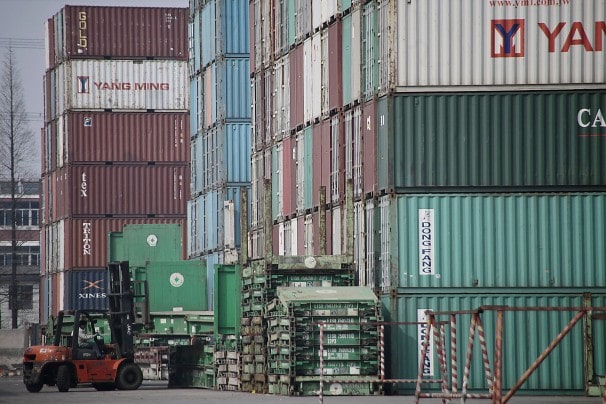
More Manufacturers Looking To Re-Shore Back To U.S.
Frank Krejci, president and CEO of Strattec Security Corp.
Master Lock LLC, Caterpillar Inc., General Electric Co. and Whirlpool Corp. have all re-shored products back to the U.S., but more manufacturers are starting to lay…
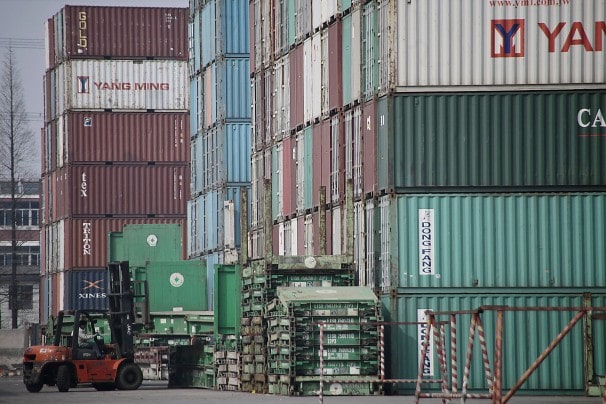
U.S. Manufacturing Becoming Low Cost
U.S. manufacturing becoming low cost over the past decade compared with factories in China, Brazil and most of the world’s other major economies.
So says a new private study, which found that rising wages and higher energy costs…
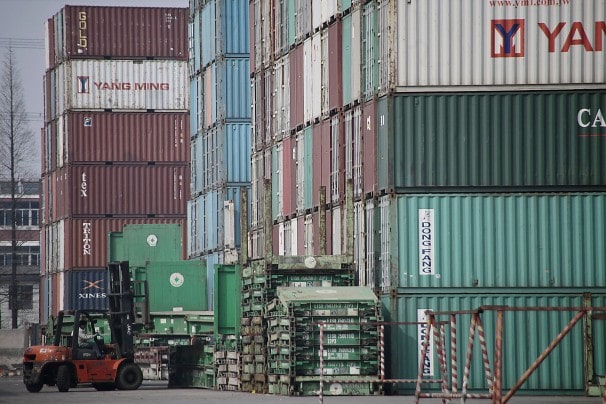
PR Ploy Or Not, Walmart’s ‘Made In America’ Push Means Something
Last week, Walmart expanded on the $50 billion Buy American pledge it made last January with a full-fledged Made-in-America summit.
That's right. Import-fueled retail giant Walmart filled a Florida convention center to…
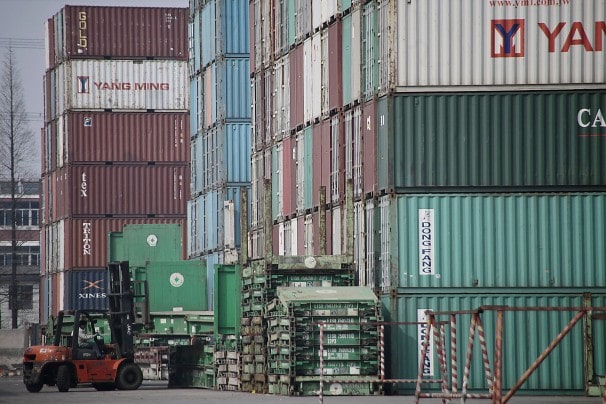
Made in USA is Back in Style For Small Businesses
Martin Rawls-Meehan, CEO of Reverie, poses at the company showroom next to a bed that reveals the manufacturing process, in Silver Creek, N.Y. The company is working to expand manufacturing in the United States. (AP Photo/David Duprey)
By Joyce…
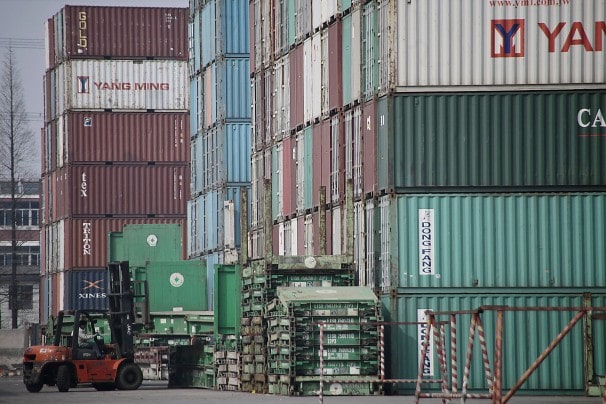
Is Reshoring a Myth or Reality?
Michele Nash-Hoff
When I first started talking about saving America manufacturing and returning manufacturing to America four years ago after the first edition of my book, Can American Manufacturing be Saved? Why we should and how…